Cover
Reinforcement shall have concrete cover (nominal) and the thickness of such cover (exclusive of plaster or other decorative finish) shall be as follows:
- At each end of reinforcing bar not less than 25 mm, or twice the diameter of such bar whichever is greater;
- For a longitudinal reinforcing bar in a column not less than 40 mm or the diameter of such bar whichever is greater. In the case of columns with a minimum dimension of 20 mm or tinder, whose reinforcing bars do not exceed 12 mm, the cover may be reduced to 25 mm;
- For longitudinal reinforcing bar in a beam not less than 25 mm or the diameter of such bar, whichever is greater;
- For tensile, compressive, shear or other reinforcement in a slab not less than I5 mm or the diameter of such reinforcement, whichever is greater; and
- For any other reinforcement not less than 15 mm or the diameter of such reinforcement, whichever is greater.
Note – The values of cover suggested are nominal cover as specified in the drawings. The cover shall in no case be reduced by more than one-third of the specified cover or 5 mm whichever is less. During construction it is essential to ensure that these tolerances are met.
- Increased cover thickness may be provided when the surfaces of concrete members are exposed to the action of harmful chemicals (as in the case of concrete in contact with earth contaminated with such chemicals), acid, vapour, saline atmosphere, sulphurous smoke (as in the case of steam-operated railways), etc, and such increase of cover may be between I5 and 50 mm over the values given in 4.1 above as may be specified by the Engineer-in-Charge. However, in no case cover should exceed 75 mm.
- For reinforced concrete members of marine structures totally immersed in seawater, the cover shall be 40 mm more than that specified in 4.1, but total cover should not exceed 75 mm.
- For reinforced concrete structures/ structural members, periodically immersed in seawater or subject to sea spray, the cover of concrete shall be 50 mm more than that specified in 4.1, but total cover should not exceed 75 mm.
- For concrete of grade M25 and above, the additional thickness of cover specified in 4.1.1 to 4.1.3 may be reduced by half.
Development of Stress in Reinforcement
- Development Length of Bars in Tension or Compression – The calculated tension or compression in any bar at any section shall be developed on each side of the section by an appropriate development length or end anchorage or by a combination thereof.
Note – Development length is the embedded length of reinforcement required to develop the design strength of the reinforcement at a critical section. Critical section for development of reinforcement in flexural members are at points of maximum stress and at points within the span where adjacent reinforcement terminates, or is bent. Provisions of 4.6.3 (c) should be satisfied at simple supports and at points of inflection.



- Design bond stress in limit state design method for plain bars in tension shall be as follows:

For deformed bars, these values shall be increased by 60 percent. For bars in compression, the values of bond stresses for bars in tension shall be increased by 25 percent.
Anchoring Reinforcing Bars
It is important to note that when a bar is subjected to both tension and compression, the anchorage value should correspond to the one which gives the maximum value, and at the same time individual requirements (with respect to tension and compression) are also satisfied as specified in 4.3.1 to 4.3.3.
- Anchoring Bars in Tension
Deformed bars may be anchored in straight lengths (without end anchorages), provided the development length requirements are satisfied. Plain bars should not be normally anchored through straight lengths alone and should be provided with hooks.
Bends and hooks
a) Bends – The anchorage value of a standard bend shall be taken as 4 times the diameter of the bar for each 45 degree bend subject to a maximum of 16 times the diameter of the bar.
b) Hooks – The anchorage value of a standard U-type hook shall be equal to 16 times the diameter of the bar.
The anchorage values of standard hooks and bends for different bar diameters are given in Table 4.1.
- Anchoring Bars in Compression
The anchorage length of straight bar m compression shall be equal to the development length of bars in compression as specified in 4.2.2. The projected length of hooks, bends and straight lengths beyond bends, if provided for a bar in compression, should be considered for development length (see Fig. 4.1).
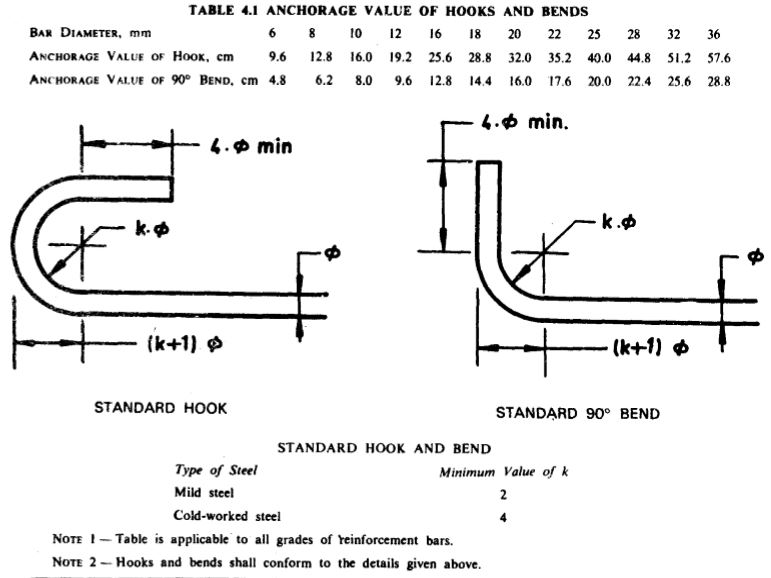
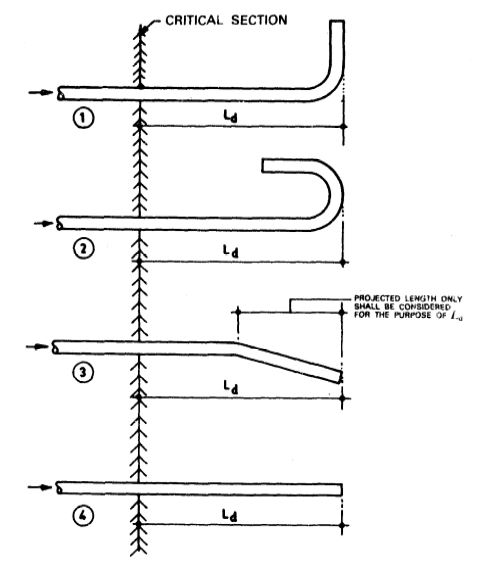

- The development length values for fully stressed bars in tension as well as compression based on 4.2.2 are given in Tables 4.2, 4.3 and 4.4.
NOTE- If the amount of steel provided at a design section is more than that required from design consideration, the development length given in Tables 4.2, 4.3 and 4.4 may be modified as:
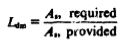
Unless otherwise specified, Ldm modified development length should be used in detailing reinforcement.
- Mechanical Devices for Anchorage – Any mechanical or other device capable of developing the strength of the bar without damage to concrete may be used as anchorage with the approval of the Engineer-in-Charge.
- Anchoring Shear Reinforcement
a) Inclined bars – The development length shall be as far bars in tension; this length shall be measured as under:
- In tension zone, from the end of the sloping or inclined portion of the bar (See Fig. 4.2A), and
- In the compression zone, from the mid depth of the beam (see Fig. 4.2B).
b) Stirrups and ties-Not withstanding, any of the provisions of this Handbook, in case of secondary reinforcement, such as stirrups and transverse ties, complete development length and anchorage shall be deemed to have been provided when the bar is bent through an angle of at least 90 degree round a bar of at least its own diameter and is continued beyond the end of the curve for a length of at least eight diameters, or when the bar is bent through an angle of 135 degree and is continued beyond the end of the curve for a length of at least six bar diameters or when the bar is bent through an angle of 180° and is continued beyond the end of the curve for a length of at least four bar diameters.
Adequate end anchorage shall be provided for tension reinforcement in flexural members where reinforcement stress is not directly proportional to moment, such as sloped, stepped or tapered footings, brackets, deep beams and members in which the tension reinforcement is not parallel to the compression face.
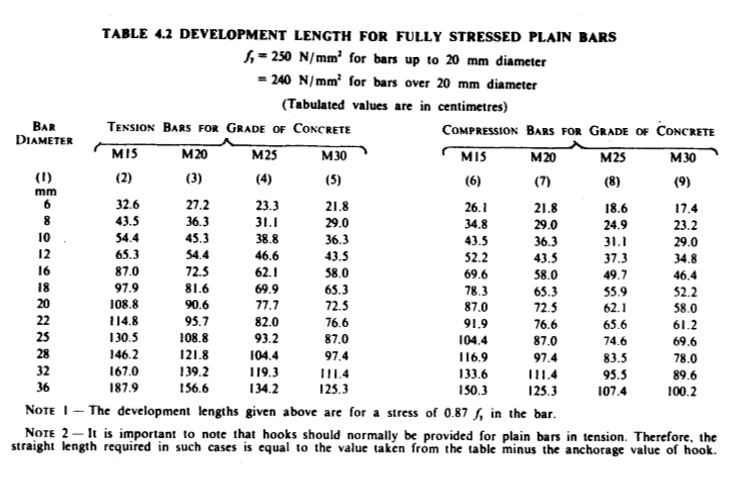
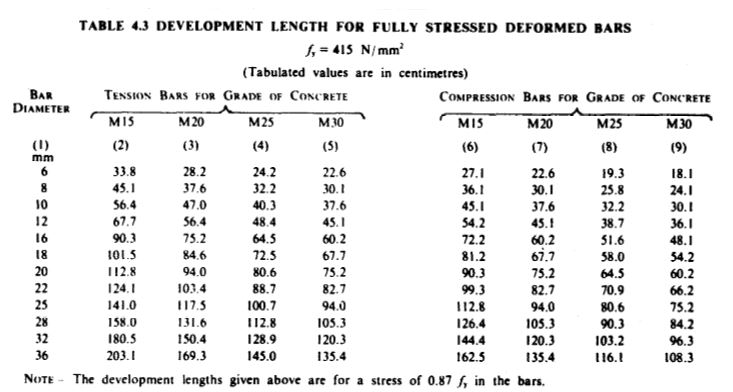

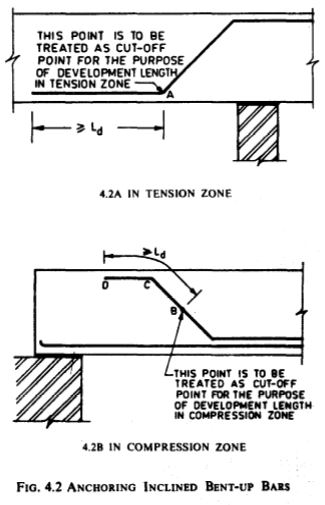
Reinforcement Splicing
- Splicing is required to transfer force from one bar – t,o another. Methods of splicing include lapping (see 4.4.2), welding and mechanical means (see – 4.4.3)
- Where splices are provided for continuity in the reinforcing bars (tension bars in beams), they shall be as far as possible away from the sections of maximum stress and be staggered. It is recommended that splice in flexural members should not be at sections where the bending moment is more than 50 percent of the moment of resistance of the section. Not more than half the bars shall & spliced at a section.
- Where more than one half of the bars are spliced at a section or where splices are made at points of maximum stress, special precautions shall be taken, such as increasing the length of lap and/or using spirals or closely spaced stirrups around the length of the splice.
Note 1 – The stirrups provided should be able to resist a tension equal to the full tensile force in the lapped bars and should be provided in the outer one-third of the lap length at both ends with at least three stirrups on either side (see Fig. 4.3). In case of thick bars (say diameter > 28 mm), lap splices should be completely enclosed by transverse reinforcement, for example, in the form of small compact stirrups or spirals [see Fig. 4.4 (A and B)].
Note 2 – Careful detailing is necessary when reinforcements are to be spliced. Therefore location and details of splices should be determined at the design stage itself and indicated in the drawing. Preferably splicing details should not be left to be decided at the site of construction.
Lap Splices
- Diameter of bars for lap splicing – Lap splices shall not be used for bars larger than 36 mm. For larger diameters, bars may be welded (see Appendix A). In cases where welding is not practicable, lapping of bars larger than 36 mm may be permitted, in which case additional spirals should be provided around the lapped bars (see Fig. 4.4A).
- Staggering of lap splices – Lap splices shall bc considered as staggered if the centre-to centre distance of the splices is not less than 1.3 times the lap length (see Fig. 4.5) calculated as given in (c) below. Bars could be lapped vertically one above the other or horizontally, depending upon the space requirement.
- Lap length in tension – Lap length including anchorage value of hooks in flexural tension shall be Ld or (30 x diameter) whichever is greater and for direct tension 2 Ld or (30 x diameter) whichever is greater. The straight length of the lap shall not be less than (15 x diameter) or 200 mm, whichever is greater (see Fig. 4.6).
where Ld= development length
Note- Splices in direct tension members shall be enclosed in spirals made of bars not less than 6 mm in diameter with pitch not more than IO cm. Hooks/bends shall be provided at the end of bars in tension members (see Fig. 4.4C).
4. Lap length in compression – The lap length in compression shall be equal to the development length in compression calculated as in 4.2.2 (see Tables 4.2, 4.3 and 4.4), but not less than 24 x diameter.
5. Requirement of splice in a column – In columns where longitudinal bars are offset at a splice, the slope of the inclined portion of the bar with the axis of the column shall not exceed 1 in 6, and the portions of the bars above and below the offset shall be parallel to the axis of the column. Adequate horizontal support at the offset bends shall be treated as a matter of design, and shall be provided by metal ties, spirals, or parts of the floor construction. Metal ties or spirals so designed shall be placed near (not more than 8 x diameter) from the point of bend. The horizontal thrust to be resisted shall be assumed as 1.5 times the horizontal component of the nominal force in the inclined portion of the bar (see Fig. 4.7). Offset bars shall be bent before they are placed in the forms. Where column faces are offset 75 mm or more, splices of vertical bars adjacent to the offset face shall be made by separate dowels overlapped at specified about.
Note – It is to be noted that in Fig. 4.7. additional stirrups will be required only near the bottom crank.
6. Bars of different diameters – When bar of two different diameters are to be spliced, the lap length shall be calculated on the basis of diameter of the smaller bar.
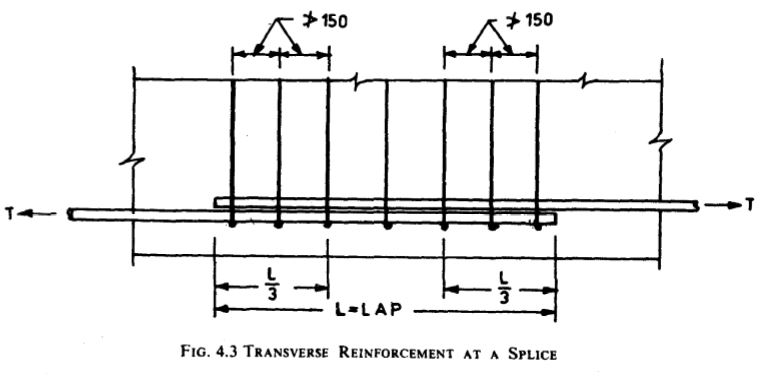
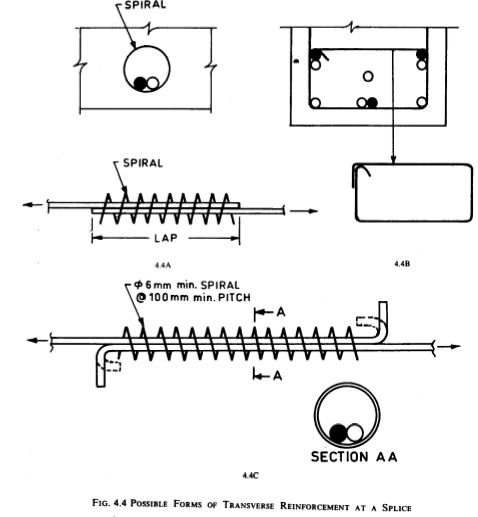
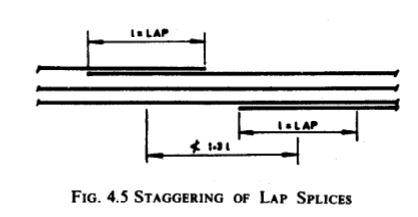
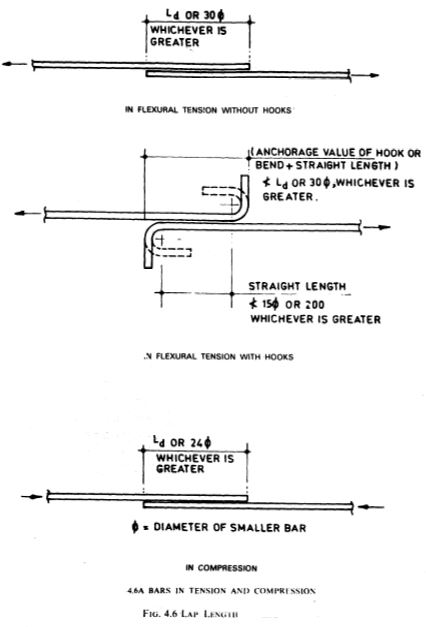
Lap splices in welded wire fabric:
- The fabric is supplied in long mats/rolls and it is rarely necessary to have a joint of the main wires. The rigidly connected cross-members provide mechanical anchorage. Adequate lapping where necessary may be provided with a comparatively short lap when cross wires occur within the lap.
- In structural slabs, laps in regions of maximum stress shall be avoided. Such splices, where used for either end or edge laps. shall be made so that the distance between outermost cross wires is not less than the spacing of the wire parallel to the lap plus 100 mm (see Fig. 4.6).
- In other cases for end laps, welded wire fabric shall be lapped not less than one mesh plus 50 mm, that is, the length of the lap shall be 50 mm greater than the spacing of wires parallel to the lap. For edge laps, a lap of 50 mm is sufficient (see Fig. 4.6).
- These requirements for lapping should be covered by suitable notes in the general specifications. But whether specified by wordings or shown on plans, certain dis- tinction should be made between ‘edge laps’ and ‘end laps’.
- The width of an edge lap shall be indicated as the centre-to-centre distance between the outside of longitudinal salvage wires of the overlapping sheets as illustrated in Fig. 4.6.
- The length of an end lap shall be indicated as the top-to-top distance between the ends of the longitudinal wires of the overlapping sheets.
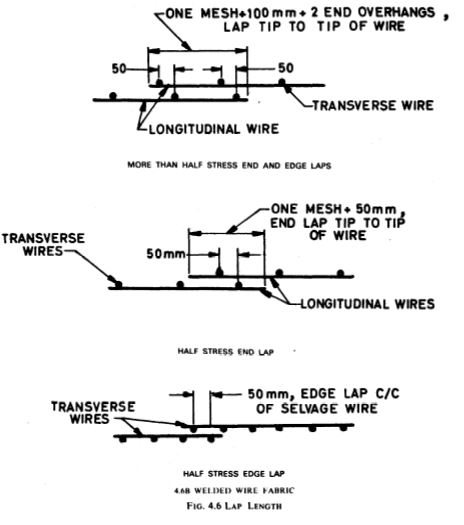
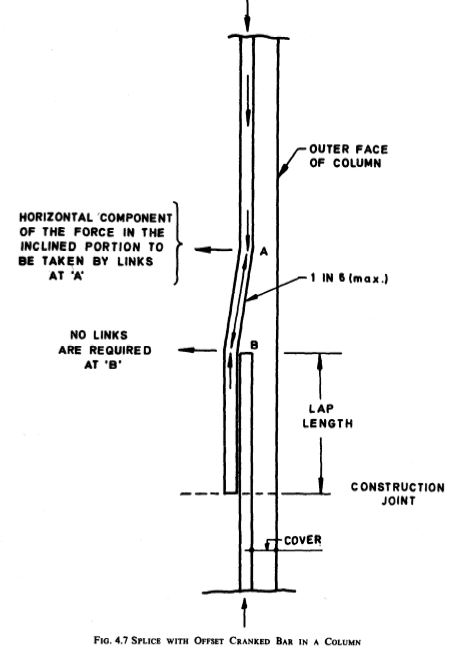
Welded Splices and Mechanical Connections:
Where the strength of a welded splice or mechanical connection has been proved by tests to be at least as great as that of the parent bar, the design strength of such connections shall be taken as equal to 80 percent of the design strength of the bar for tension splice and 100 percent of the design strength for the compression splice. However, 100 percent of the design strength may be assumed in tension when the spliced area forms not more than 20 percent of the total area of steel at the section and the splices are staggered at least 600 mm centre-to-centre.
The choice of splicing method depends mainly on the cost, the grade of steel, the type of reinforcement, generally high bonding, the possibility of transferring compressive and/ or tensile stresses and the available space in the section concerned. The designer shall specify the splicing method and the conditions under which it is to be carried out.
Mechanical coupling devices shall be arranged so that as small a number as possible affect a single section.They should, in addition, be placed outside the most highly stressed sections.
Sleeve splicing – If correctly used, sleeve connections may transmit the total compressive or tensile stress. In general, the use of these sleeves is governed by various conditions laid down in the agreement for the method or, in the absence of recommendations, by preliminary testing.
During assembly, particular care shall be taken to ensure that the lengths introduced into the sleeve are sufficient.
These lengths should be marked before hand on the ends of the bars to be spliced except when a visual check on penetration is possible (for example, sleeve with a central sight hole):
a) Threaded couplers (see Fig. 4.8)
In order to prevent any decrease in the end sections of the bar as a result of threading (with V- form or round threads), they can be: 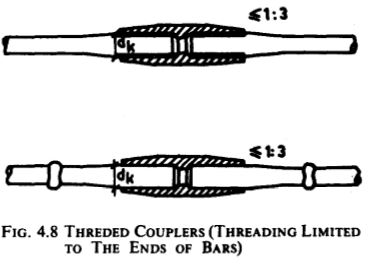
1) upset;
2) for long units, fitted with larger section threaded ends by flash welding; or
3) fitted with a threaded sleeve by crimping.
Another solution consists of threading the ends but only taking into consideration the nominal section of the threaded end, that is, reducing the permissible stress in the reinforcement.
The ends of the sleeve shall be slightly reduced in section, in order to prevent overstressing of the first few threads.
There are, at present, reinforcing bars with oblique, discontinuous., spiral ribs, allowing splicing with a special sleeve with internal threads.
This same process is used to splice prestressing bars, and in order to prevent confusion between reinforcing bars and prestressing steels, the direction of threading is reversed (see Fig. 4.9).
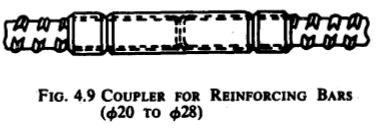
Two lock nuts. tightened on each side of the sleeve into which the reinforcing bars are introduced to the same depth, prevent -any accidental unscrewing due to slack in the threads (splices not under tension). The nuts are tightened with a torque wrench. This device is also used for splicing prefabricated elements. These joints are generally 100 percent efficient under both tension and compression. To decrease the itt-siru operations. one of the ends is generally fitted with its sleeve in advance and the other bar to be joined with the sleeve should remain manoeuvrable until the splice has been made (see Fig. 4. 10)
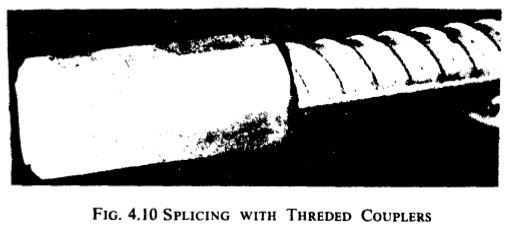
b) Coupling with a crimped sleeve
Crimped sleeves constitute a method of splicing limited to relatively large diameter deformed reinforcing bars. It consists of the introduction of the bars to be spliced into a sleeve which is crimped by means of a hydraulic crimping tool onto the ribbed bars in order to fill the voids between them and the inner surface of the sleeve. The ribs on the bar penetrate into the relatively softer steel of the sleeve and the ribs work in shear.
During crimping the sleeve lengthens, and the other reinforcing bar to be spliced should be displaceable at this moment. The size of the crimping device requires a bar interspacing of at least 10 cm (see Fig. 4.11). Splicing by crimping is also possible with reinforcing bars of differing diameter. The same method also enables threaded steel rods to be spliced to reinforcing bars using high strength threaded bolts (see Fig. 4.12).
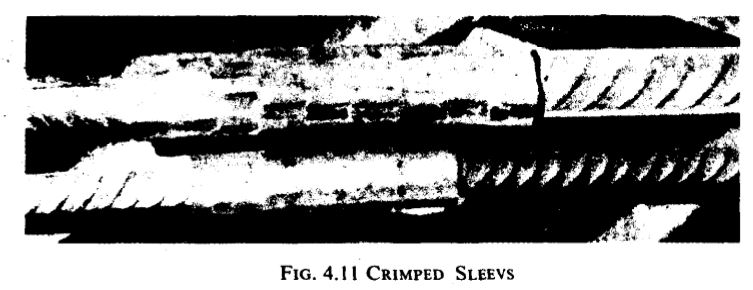
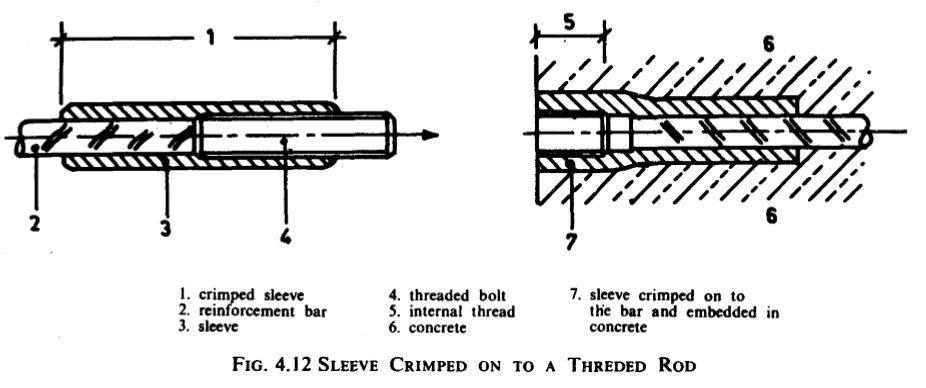
c) Coupling with injected sleeves
These couplings are a special case of sleeve splicing; the stresses are distributed by the shear strength of the product injected between the ends of the bars to be sleeve spliced:
1)With the ‘Thermit’ sleeve the space between the deformed bars and the sleeve, whose internal surface is also ribbed, is tilled with a special molten metal. This molten metal is prepared in a crucible, which is in communication with the sleeve, by igniting a mixture consisting mainly of iron oxide and aluminium powder. The strength of the sleeve may be increased by using a larger sleeve diameter (see Fig. 4.13).
The sleeve is shorter ‘but wider than that used in the crimping method. The bars are not in contact.
The splice may be made in any direction as long as space allows the crucible to be put into place.
2) Similar method is the injection of grout or an epoxy resin between the sleeve and the bars. The length of the sleeve is necessarily greater (see Fig. 4.14).
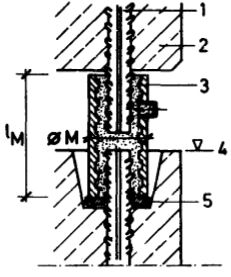
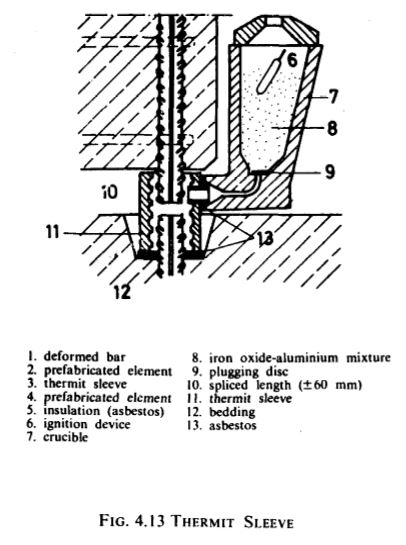
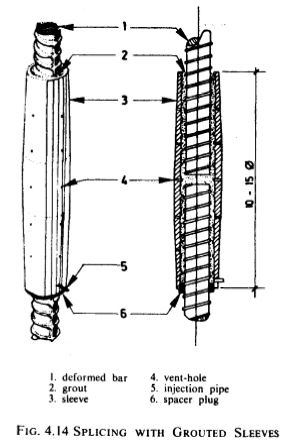
d) Butt splices – For this purpose open flanged sleeves made from steel strip can be used. They are tightened onto the bars by the introduction of a flat tapered wedge (see Fig. 4.15).
The end sections, in contact within the device, shall be perfectly at right angles to the axis of the spliced bars.
Another method involves the use of 4 small diameter ribbed bars which are tightened, using pliers, with 3 ring-clamps. The advantage of this method, in comparison to the previous one, is the fact that it allows a portion of the tensile stress to be taken up.
For bars with ribs in the form of a thread, a butt splice may be made with a sleeve, but with greater facility.
There are also sleeves consisting of a metallic cylinder, the internal diameter of which fits the bars to be spliced. This sleeve is fixed to one of the reinforcing bars by a few welding points: a hole at the centre of the sleeve enables one to check that there is contact between the bars. This economical method of splicing, which is easy to apply, can only transmit compressive stresses.
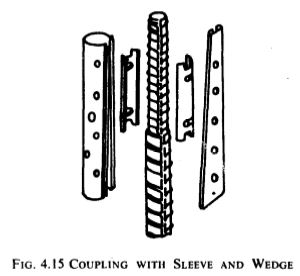
Main advantages and disadvantages of mechanical coupling:
- The use of mechanical couplers is frequently justified when space does-not allow lapping, although crimping and tightening tools require accessibility which may reduce this advantage.
- This splicing method often requires more careful cutting of the reinforcing bar, a check which is more difficult than in the case of lapping;it also requires the use of reinforcing bars of the same diameter, and mobility of one of the two bars to be spliced.
- Good performance of the splice is not endangered special atmospheric conditions as in welding.
- The cost of equipment and its use limit this method to exceptional cases only.
NOTE- Some mechanical methods of splicing of reinforcement which are in vogue in this country make use of the following principles:
a) A special grade steel sleeve is swaged on to reinforcing bars to be joined with the help of a portable hydraulically operated bar grip press either at site or at stocking yard.
b) Two sleeves with threaded ends are drawn together by an interconnecting stud. These sleeves are then swayed on to the reinforcing bars either at site or at the stocking yard.
Hooks and Bends
- Hooks and bends, and other anchorage of reinforcement in reinforced concrete shall be of such form, dimensions and arrangement as will ensure their adequacy without over-stressing the concrete or steel.
- Where normal hooks are used. they should be of U-type or L-type; but usually U-type is preferred for mild steel bars and L-type for deformed bars. If the radius of the bend or hooks conforms to that of the standard hooks or bends in longitudinal bars, the bearing stresses inside the bend in concrete need not be checked.
a) Bearing stresses at bends – The bearing stress in concrete for bends/ hooks in stirrups and ties conforming to 4.3.5(b) need not be checked as there is a transverse bar at each bend. The bearing stress inside a bend in all other cases should preferably be calculated as given in the following formula (see Fig. 4.16). The most dangerous situation is that of a bar, the layout of which is parallel to a surface or wall. Safety can be substantially increased by inclining the curve zone towards the mass of concrete wherever possible, a condition which frequently occurs in anchoring. However, it may be noted that IS: 456-1978 also exempts check for bearing stress in concrete for standard hooks and bends described in Table 4.1.
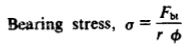

Characteristic strength of concrete and for a particular bar or group of bars in contact shall be taken as a centre-to-centre distance between bars or groups of bars perpendicular to the plane of the bend (mm); for a bar or group of bars adjacent to the face of the member, a shall be taken as the cover plus size of bar.
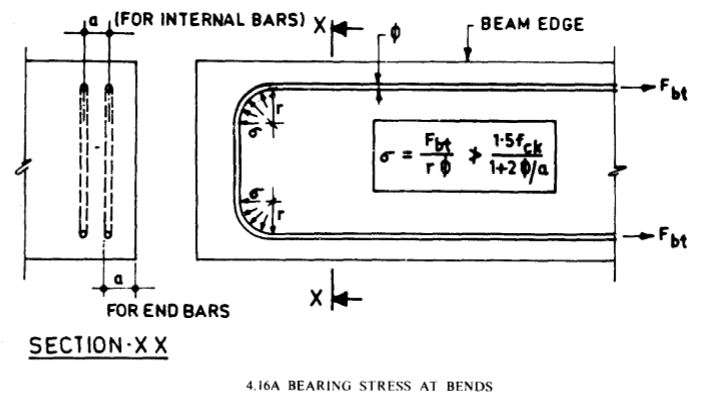
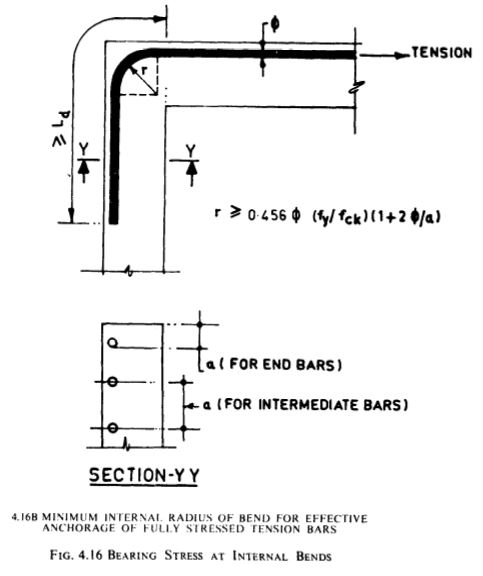
In other words, the minimum radius of the bend, r, should be such that 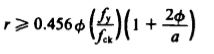
When the large steel stresses need to be developed il. ‘he bend, radial bearing stresses in the concrete may become excessive. The above equation controls the diameter of bend when there is a combination of high tensile stress in the bend. large bar diameter and low concrete strength. To simplify the application of the above formula minimum radius of bend is given in Table 4.5 for different grades of concrete and steel.
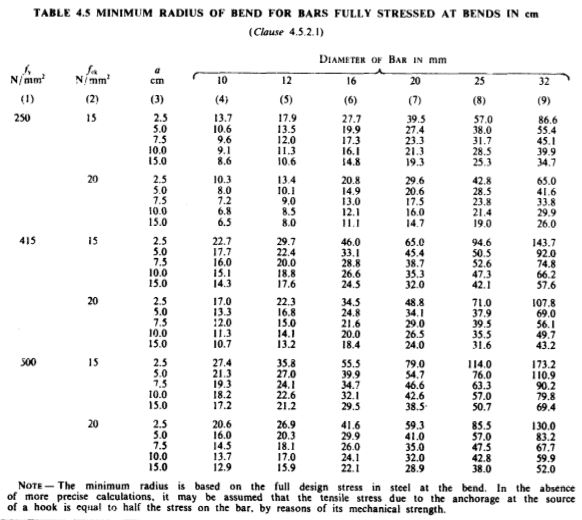
b) If a change in direction of tension or compression reinforcement induces a resultant force acting outward tending to split the concrete, such force should be taken up by additional links or stirrups. Accordingly in structural components with curved or angled soffits, or those formed with bends or corners, it should be ensured that the radial tensile forces due to changes in the direction of reinforcement are resisted by additional links (see Fig. 4.17). Bent tension bar at a re-entrant angle should be avoided.
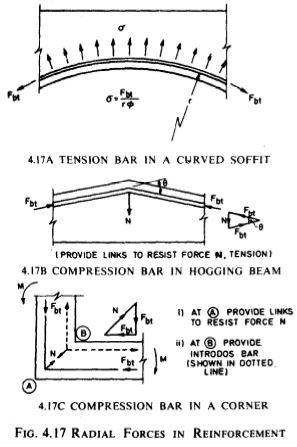
c) The minimum straight length of hook is four times the bar diameter. For small diameter bars this should be a minimum of 5O’mm in order to facilitate holding the bar in place while forming the hook. The hooks when formed are quite large and while detailing it is important to ensure that they do not foul with other reinforcement, particularly where beams have more than one row of bars.
d) Reinforcing bars shall be so detailed that the hooks are not positioned in tensile zones of concrete as this may cause cracking. It is better to bend the bars so that the hooks and bars terminate in compression zones or so lengthen the bars to eliminate the need for hooks.
Curtailment of Tension Reinforcement in Flexural Members
- For curtailment, reinforcement shall extend beyond the point at which it is no longer required to resist flexure for,a distance equal to the effective depth of the member or 12 times the bar diameter, whichever is greater, except at simple support or end of cantilever. Figures 4.18 to 4.21 illustrate the requirement at cut-off point and at supports in flexural members.
Note 1 – A point at which reinforcement is no longer required to resist flexure is where the resistance moment of the section, considering only the continuing bars, is equal to the design moment.
Note 2 -The points at which reinforcement can be curtailed is to be based\ on the bending moment envelope developed by the designer. It should be noted that the use of envelope helps in achieving better design. A typical bending moment envelope considering various loading conditions is given in Fig. 4.22.
Figure 4.23 gives a standard bending moment diagram (based on uniformly distributed load) to enable designers to choose locations for curtailment of reinforcement.
Flexural reinforcement shall not, preferably, be terminated in a tension zone unless any one of the following conditions is satisfied:
- The shear at the cut-off point does not exceed two-thirds that permitted, including the shear strength of web reinforcement provided.
- Stirrup area in excess of that required for shear and torsion is provided along each terminated bar over a distance from the cut- off point equal to three-fourths the effective depth of the member. The excess stirrup area (sq.mm) shall be not less than 0.4 bs/fy, where b is the breadth of beam (mm), s is the spacing (mm) and fy is the characteristic strength of reinforcement (N/sq.mm). The resulting spacing shall not exceed (d/8)Bb , where Bb is the ratio of the area of bars cut-off to the total area of bars at the section and d is the effective depth.
- For 36 mm and smaller bars, the continuing bars provide double the area required for flexure at the cut-off point and the shear does not exceed three-fourths that permitted.
Positive Moment Reinforcement
a) At least one-third the maximum positive moment reinforcement in simple members and one-fourth the maximum positive moment reinforcement in continuous members shall extend along the same face of the member into the support, to a length equal to Ld/3 (see Fig. 4.18). where Ld is the development length based on fully stressed bars. This is required to provide for some shifting of the moment due to changes in the loading, settlement of supports, lateral loads and other causes.
b) When a flexural member is part of a primary lateral load resisting system, the positive reinforcement required to be extended into the support according to (a) shall be anchored to develop its design stress (fully developed stress) in tension at the face of the support (see Fig. 4.19). This anchorage is to assure ductility of response in the event of unexpected over- stress such as from an earthquake. It is not sufficient to use more reinforcement at lower stresses. The full anchorage requirement does not apply to any excess reinforcement over and above that provided at the support.
At simple supports and at points of inflection, positive moment tension reinforcement shall be limited to a diameter such that Ld does not exceed (see Fig. 4.18) 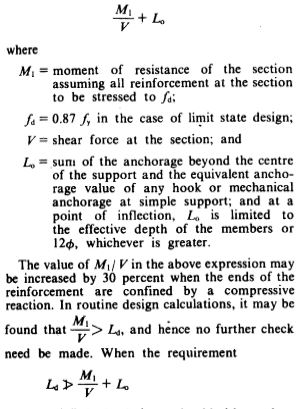
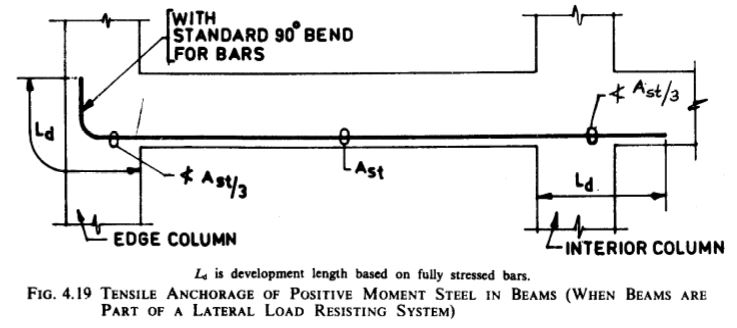
is not satisfied, the designer should either reduce the diameter of bars, whereby Ld is reduced, or increase the area of positive reinforcement at the section considered, whereby M1 is increased, or resort to botli the steps.

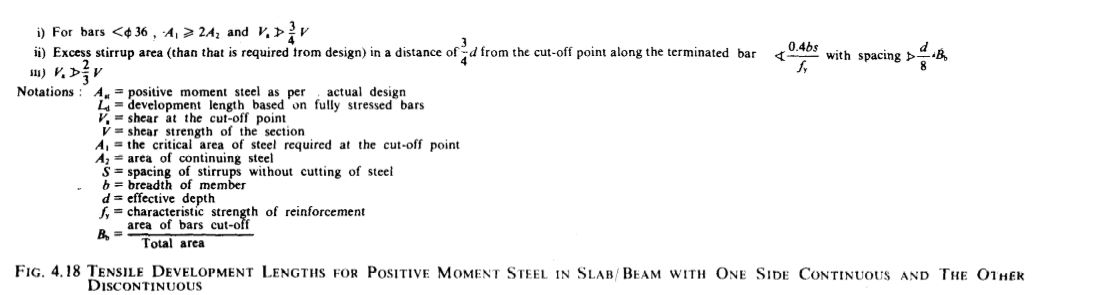
Negative Moment Reinforcement
At least one-third of the total tension reinforcement provided for negative moment at the support shall extend beyond the point of inflection (PI) not less than the effective depth of the member or 12 x diameter or one-sixteenth of the clear span, whichever is greater (see Fig. 4.20 and 4.21).
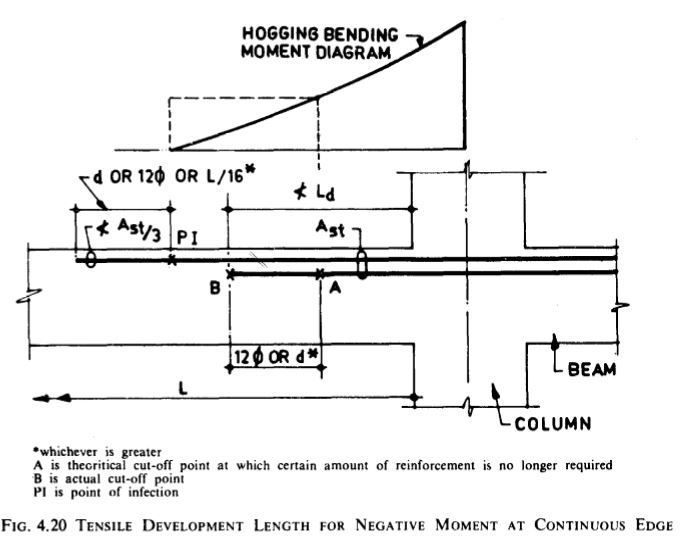
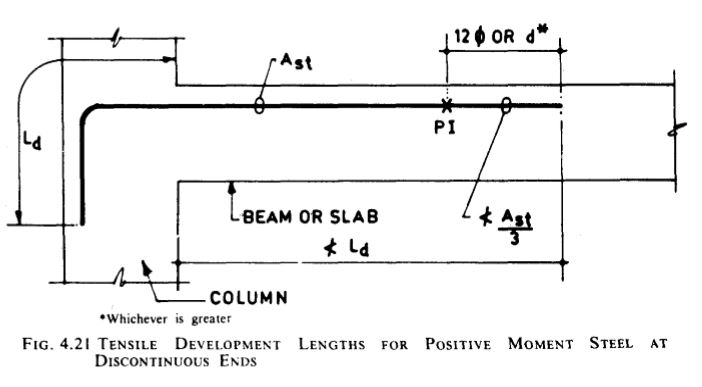
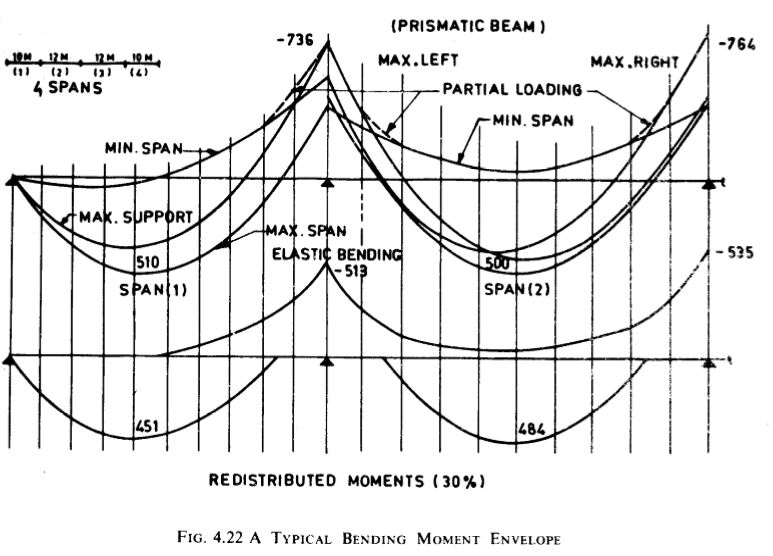

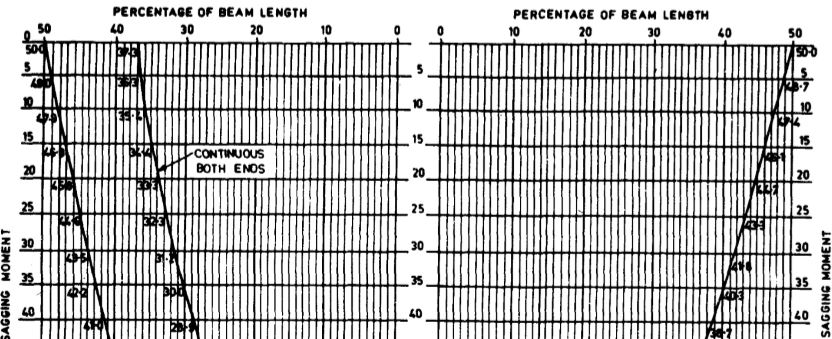

Spacing of Reinforcement
For the purpose of this clause, the diameter of a round bar shall be its nominal diameter, and in the case of bars which are not round or in the case of deformed bars or crimped bars, the diameter shall be taken as the diameter of a circle giving an equivalent effective area. Where spacing limitations and minimum concrete cover are based on bar diameter, a group of bars bundled in contact shall be treated as a single bar of diameter derived from the total equivalent area.
Bars Bundled in Contact
General – Bars in pairs, or in groups of 3 or 4 tied together and in contact side by side (bundled bars) may be used in beams and columns. This has been the practice in USA for many years, and is now permitted in most countries including India.
As bundled bars provide more reinforcement in less space than do single bars, it is possible to reinforce a member more heavily and still get better compaction of concrete. Beam and column sizes can thus often be reduced with saving in cost.
Bundled bars shall not be used in members without stirrups. Bundled bars shall be tied together to ensure the bars remain together as a bundle. Bars larger than 36 mm diameter shall not be bundled except in columns.
Whenever bar spacing limitations, minimum cover, tie size and spacing are based on bar diameter, a group of bars bundled in contact shall be treated as a single bar of diameter derived from the total equivalent area (see Table 4.6). However, the cover provided should be measured from the actual outside contour of the bundle.
Note 1- Unless patented splices are used, the bundling of bars in columns is not recommended, as all joints have to be staggered. However, even when patented splices are used the necessary staggering of splices makes assembly difficult and prefabrication cumbersome.
Note 2- It is recommended to limit the bundle only to two bars or three bars as four bars many times do not tie into a stable bundle.
Development Length
Ld of each bar of bundled bars shall be that for the individual bar, increased by IO percent for two bars in contact, 20 percent for three bars in contact and 33 percent for four bars in contact. The anchorages of the bars of a bundle can only be straight anchorages.
Curtailment
Bars in a bundle shall terminate at different points spaced apart by not less than 40 times the bar diameter except for bundles stopping at a support (see Fig. 4.24)
Splicing
In case of bundled bars, lapped splices of bundled bars shall be made by splicing one bar at a time, such individual splices within a bundle shall be staggered. For bundles of 2, 3 or 4 bars, the staggering distance should be 1.2, 1.3 and 1.4 times the anchorage length of the individual bars respectively.
